Yaskawa solutions to make electric mobility production processes more flexible.
The collaboration between Lazpiur and Yaskawa has enabled the development of an innovative and effective solution that not only meets the highest industry standards, but has also boosted the competitiveness of a company focused on developing solutions for the electric mobility sector.
- Industrije
- Elektronika
- Avtomobilska industrija
- Aplikacije
- Material Handling
- Quality Inspection
- Stranka
- Lazpiur
- Izdelki
- GP25 - GP - serija
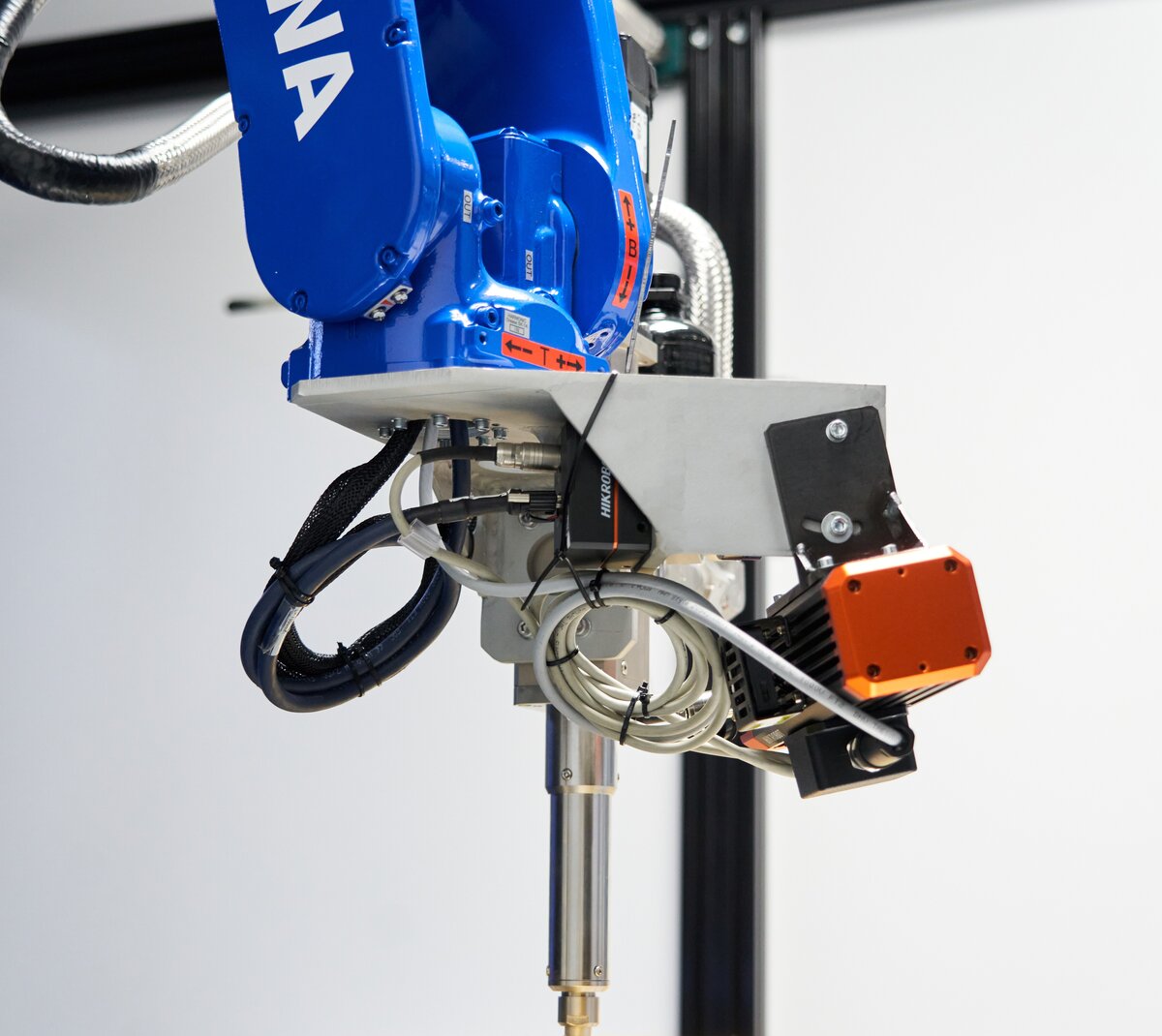
Lazpiur, engineering solutions for more flexible productio
This was the case of a company dedicated to the design and manufacture of machines and assembly lines specialising in electronics and batteries for automobiles which, in its bid to achieve the most efficient production possible, decided to take on the challenge of developing a flexible dispensing machine capable of processing both battery modules and complete packs, adapting to any cell morphology used in the industry.
With this goal in mind, they relied on the experience of Lazpiur, a company with more than a century of history that has always stood out for its commitment to innovation and precision in the creation of advanced technological solutions. Lazpiur's highly specialised team quickly detected that the main challenge of the project lay in designing a multi-technology production cell capable of performing a quality inspection of the dispensing in different situations and battery references.
A competitive and flexible solution thanks to Yaskawa's GP25 robot.
They needed the cell to be equipped with a robot with high reach and load capacity, and the GP25 robot from Yaskawa, a world-leading manufacturer of servos, motion controllers, AC motor drives, switches and industrial robots, was chosen.
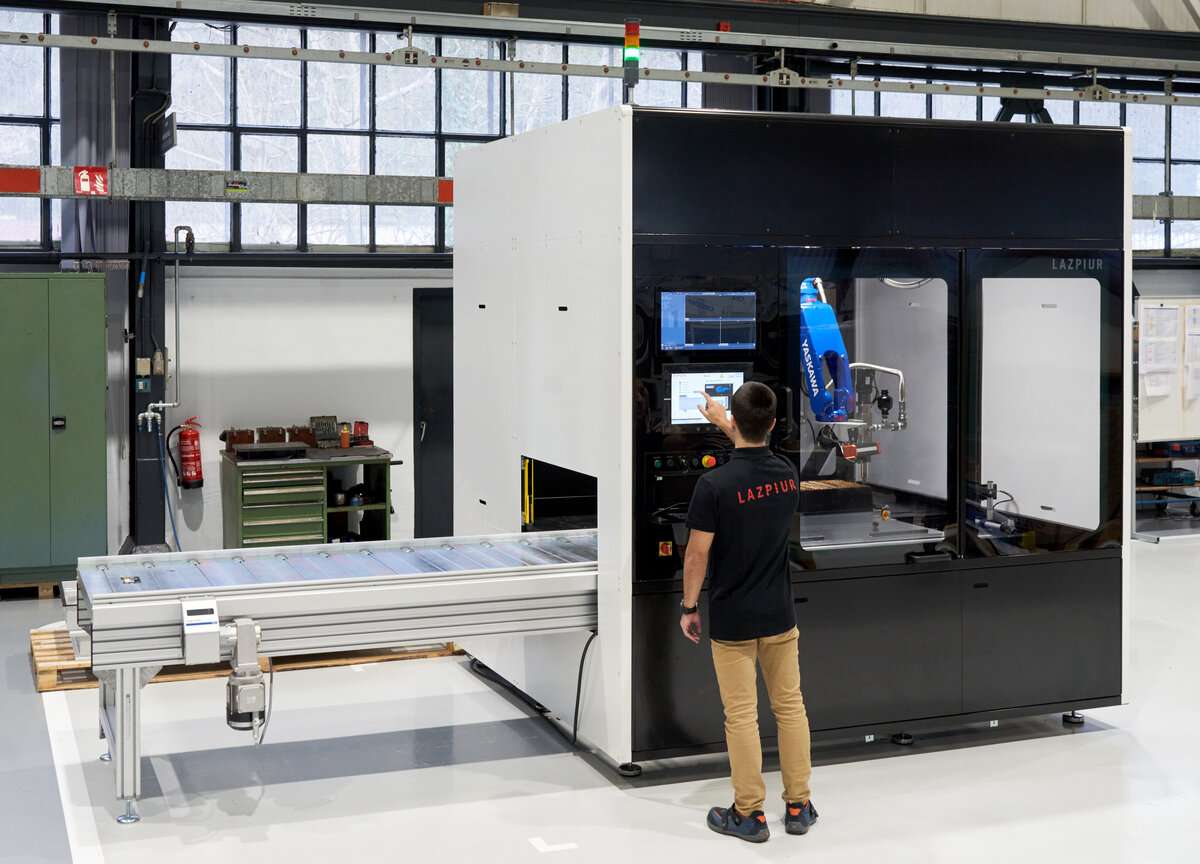
Immediate results for continued success.
The end result of the project was the creation of a compact and highly competitive cell, designed to handle medium workloads in multi-reference environments, which provided the company with a number of benefits including:
Greater flexibility: to achieve the main objective of the project, the ability to adapt to different battery and battery module references and thus ensure efficient and adaptable production.
Competitiveness: compared to traditional dedicated production cells, the adaptability of this solution is, in itself, a significant advantage in such a competitive market.
Advanced machine vision: the integration of flexible machine vision software offers the ability to manage multiple references and guarantee dispensing quality.
High degree of integration: full traceability at plant level enables comprehensive production tracking. A key feature to ensure process quality at every stage.