Swisstex - Synthetic fibre spinning
- Industrije
- Textile
- Stranka
- SwissTex
Consistent speed critical for quality
Inverter drives from Yaskawa ensure high process reliability in the production of technical synthetic fibres
In the production of thermoplastic fibres and yarns, it is necessary to ensure that the key parameters remain consistent and within strict tolerance limits over long periods of time. This applies, among other things, to the drives for extruder screws, the pumps for spinning the individual filaments, the cooling, texturing and drawing stations as well as the winders. Thanks to their special properties, textile machine manufacturer SwissTex uses Yaskawa inverter drives to control drive speed in its applications.
When textiles are used in technical applications, it is preferable to use synthetic fibres because of their special properties. Textiles are used in a variety of areas, from safety belts, tarpaulins, parachutes and airbags to heavy-duty carpets for buildings and vehicle interiors and the reinforcement cord used in tyres and conveyor belts. The benefit of using man-made fibres is that their properties can be modified during the production process. Such textiles can therefore be tailored to meet the specific needs of their intended use.
Sophisticated complete systems
SwissTex, based in Winterthur in Eastern Switzerland, is a global manufacturer of synthetic fibre spinning machines. As a system provider, the company develops process technology and realises complete systems that accommodate the operator’s structural requirements. This includes the extruders, spin beams, drawing machines, texturing stations and winders used in yarn production. The company’s systems are used to produce fibres and yarns from thermoplastic materials such as polyamide (PA), polypropylene (PP) and polyesters (e.g. PET). An extruder fuses the plastic granulate. This molten mass is then pressed through spinnerets using metering pumps. The systems are adjusted to suit the thermoplastic being used and are designed so that individual filaments from the spinnerets are air-cooled before being discharged vertically downwards. The filaments are then combined into fibre strands, or yarn. Depending on the structure of the system, two or more fibre strands run in parallel. With this design, it is possible to produce multi-coloured yarns using fibres of different colours. The yarn is then fed across several stretching devices called galettes in a drawing machine. The galettes move at different speeds, thereby mechanically drawing the yarn and giving it the desired properties. Yarn for carpets then undergoes a texturing process. At the end of the process, automatic winders create spools of yarn.
Inverters for all drive specifications
At every stage of production, it is critical that parameters – once they have been optimised and set – are maintained within strict limits over a long period of time. This applies in particular to the electrical drives at different stations. Extruders, for example, may have AC motors with an output between 30 kW and 150 kW. To set and maintain precise speeds regardless of the load, the textile machine manufacturer controls its motors using YASKAWA inverter drives from the A1000, V1000 and T1000 series.
These units offer numerous advantages and, as robust industry-standard hardware, are available both at short notice and in large quantities. They have also been awarded with all international electrical and electromagnetic inspection approvals, licences and certificates, including cUL, UL and CE. This is crucial for a company like SwissTex because spinning machines from Switzerland are exported all over the world. In addition, Yaskawa comprehensive product portfolio includes units designed for the entire output range from 0.5 kW to 630 kW. This enables textile machine manufacturers to purchase inverter drives for all of the drives in their synthetic fibre spinning machines from a single manufacturer. Depending on the design of the system, this could mean up to 60 units at each production plant. As SwissTex shows, by concentrating on a single manufacturer, it is possible to simplify the logistics of purchasing drive technology. This approach minimises the cost and labour involved in project planning, design and spare part logistics. It also makes it possible to achieve a high level of efficiency in a market that is heavily influenced by cost-related factors. For the operators of spinning machines, another important advantage is that spare parts are available at short notice when required.
Easy commissioning and replacement with soft parameters
Another beneficial feature of Yaskawa inverters is the sophisticated software, which is specific to each application. This enables operators to set variable parameters for the functions of the unit in a broad range of areas. The inverters can thus be adjusted to accommodate diverse process requirements. With efficient auto-tuning functions, the units automatically determine the necessary motor parameters, thus ensuring ideal motor control and running properties. As an additional benefit, the units can be programmed quickly, easily and securely using a remov-able memory device (USB stick, laptop or copy unit); they can also be programmed fully automatically via a communication interface. This lowers costs and reduces possible sources of error in production and startup. In the unlikely case that a customer’s unit needs to be replaced, this can also be accomplished quickly, easily and securely thanks to a patented terminal board. It is not necessary to program the new unit because the parameters are stored on this terminal board. Since this greatly minimises downtimes, it is an important factor in achieving efficiency – particularly for cost-Yaskawa systems such as spinning machines, which are in use around the clock (24/7) without interruption.
Outstanding synchronisation
SwissTex also uses Yaskawa A1000 and V1000 inverter drives for the drive motors connected to galettes. In this case, machine manufacturers profit from outstanding synchronisation when controlling electric motors with these inverters. For fibre processing speeds of 4000 m/min or more, the speed of each galette has to be regulated so that it does not deviate from the set parameter by more than 1 m/min. For the drives of the draw rolls, it must be possible to synchronise the individual drives with extreme precision so that they remain perfectly coordinated. This is required to generate the necessary tensile forces between rolls. To save energy, the DC buses of the inverter drives share an electrical connection. The power from drives running on generator power can thus be transferred to the remaining drives. Nowadays, it is only possible to achieve the necessary quality of yarn while maintaining consistent properties – such as filament diameter and tensile strength – when the speed of the electrical drives is controlled with extreme precision. This also applies to winding machines that spool the yarn after it has been produced. At this stage of production, it is critical that the speed of the spindles is constantly adjusted in line with the increasing diameter of the yarn being spooled. YASKAWA inverter drives are also perfectly suited to this task as they always maintain the precise speed profile that has been set. Current winding machines are switched fully automatically with no interruption to yarn production.
Process reliability through configuration with CANopen
Another reason why the technicians at SwissTex chose inverter drives from the V1000 and A1000 series was their universal technology. Signals from external sensors, for example, can be fed in via digital and analogue I/Os or standard interfaces to control the units. The technicians at SwissTex use the CANopen fieldbus to transfer data between the inverter drives and the central machine controller. This has a number of advantages when installing the inverter and, if applicable, when replacing the unit. When the power is switched on, the central controller transmits the complete set of drive-specific parameters to the inverters. This increases process reliability and reduces idle times in the event of technical problems. Not only does it eliminate the need for elaborate parameter configuration, but it also prevents personnel from causing malfunctions by operating the control displays on the inverters by accident or without permission.
As SwissTex reports, the Yaskawa inverters in the spinning machines have delivered excellent performance for over seven years. SwissTex also praises the customer service and technical support provided by Yaskawa when the inverters were integrated in the mechanical and control environment. Furthermore, SwissTex is confident that Yaskawa units operate reliably all around the world under even the most difficult operating conditions. In fact, over a period of several years, employees could recall only a few occasions when a technical service call became necessary as a result of a defective inverter.
Results
- Cost reduction and logistic process enhencements by using 1 Supplier for all drive compontents
- Wide product range with ratings from 0,5 to 630 kW
- Easy setup and maintenance characteristics
- Outstanding synchronisation
- Process reliability through configuration with CANopen
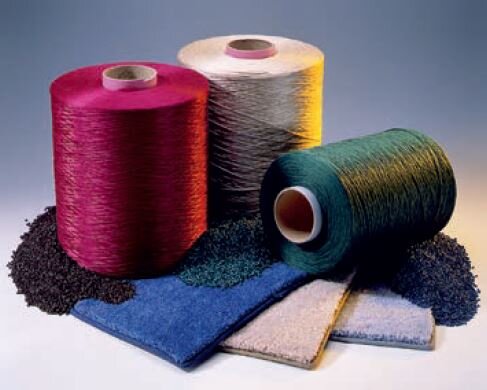