Servo technology for greater performance
Protecting chair castors saves packaging
Saving on packaging has become a hot topic, even for bulky objects such as office chairs. To make sure these goods reach the customer undamaged, their castors can be protected with plastic caps. It is then sufficient to simply cover the chairs during transport, dispensing with the need for cumbersome cardboard. The chair and furniture castor specialist Gross+Froelich relies on modern automation technology to apply its ring-shaped protective caps. Sigma-7-series servodrives and a SLIO-series controller from Yaskawa play a key role in this process.
Anything that has castors doesn’t have to be carried. Of course, that doesn’t mean that your typical office chair is pushed all the way to the customer, but the chair’s castors can certainly be used to transport them from the truck to the parking lot to the office desk. To ensure that they arrive there without any scratches, however, the castors must be protected. Plastic caps are a good solution for doing so. After transport, they are easy to remove and recycle. But how are the protective caps put on the chair castors?
- Aplikacije
- Picking | Packing
- Assembly
- Stranka
- Gross+Froelich GmbH & Co. KG
- ARAMIS Maschinenbau GmbH & Co. KG
Up to 36,000 caps per day
A chair castor basically consists of two individual wheels, with a cap pressed onto each. This process is performed fully automatically and at considerable speed. Gross+Froelich in the small town of Weil der Stadt in Germany uses a machine made by ARAMIS Maschinenbau GmbH & Co. KG that now operates with cycle times of 2.4 seconds following its redesign with servo technology. Depending on the castor model, that means that up to 36,000 ring-shaped protective caps are applied fully automatically to the wheels in 24 hours of operation, which are then connected to form the complete castor further on in the assembly process. That’s around 10,000 caps more than the machine managed before the redesign.
Electrical power instead of pneumatics
Just two measures were basically enough to achieve the shorter cycle times: The capacity of the rotary indexing table for the plastic caps was increased from four receptacles to eight. In addition, three of the pneumatic drives installed in the machine were replaced by highly dynamic electrical servo drives. It would have been practically impossible to achieve the higher speeds with pneumatic drives, because the mechanical stress would have become excessively high. Furthermore, the level of compressed air consumption is much lower, with a positive effect on operating costs.
The Sigma-7 series from Yaskawa was chosen for the electric drives. They have already proven themselves in many similar applications, and impressed the machine builder ARAMIS. After all, some of the defining features of the Sigma-7 series include rapid commissioning, high production capacity and maximum operational reliability. In addition, the responsive AC servo motors feature extremely compact dimensions and are very quiet to run. They offer high resolution (with an integrated 24-bit absolute encoder) and high dynamics. Features such as vibration suppression, suppression of machine resonance frequencies and a tuningless function for simple startup are integrated into the compact servo amplifiers.
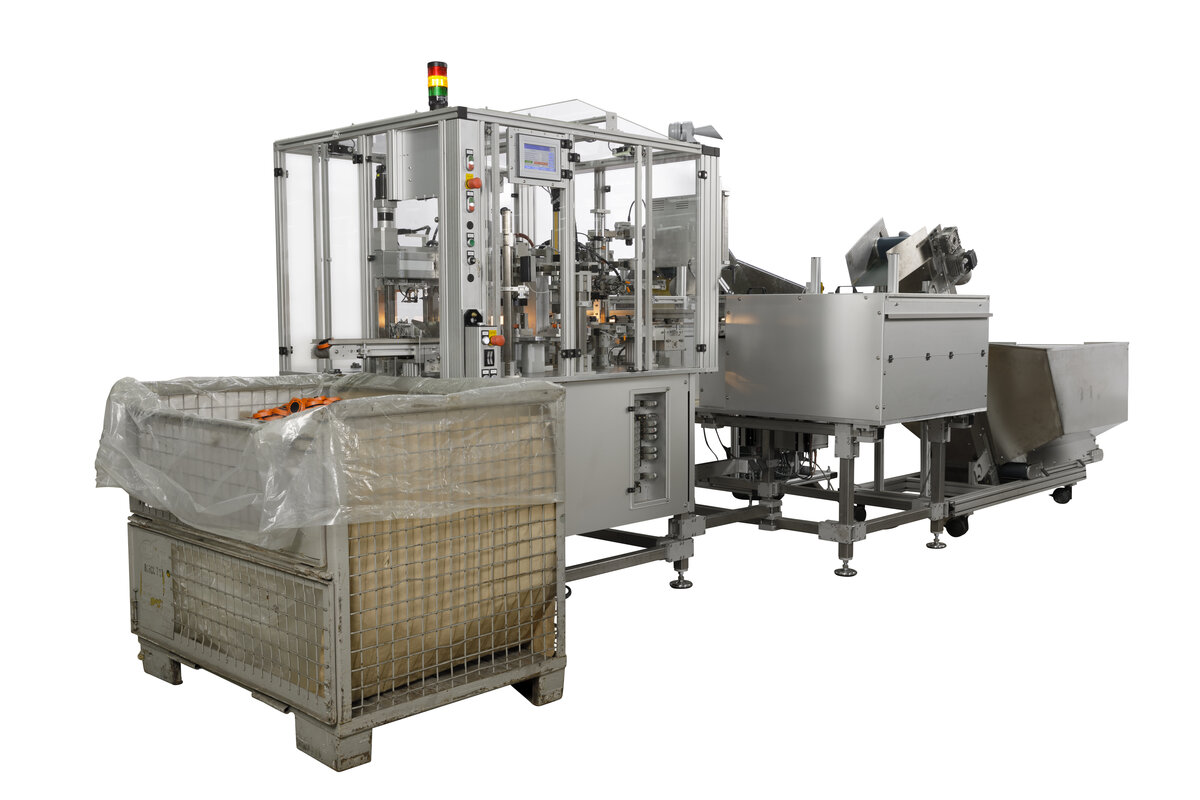
The machine builder, its electrical design partner and the company Roggenstein Elektronik worked together with automation specialists from Yaskawa to retrofit the machine for fitting the protective caps. A total of three 400 V servo axes, each with 400 W of power, are now in use in the machine: One drive is responsible for the horizontal movement of the feed. A pneumatic linear unit with a gripper transfers the plastic cap from the separation unit to the nest of the rotary table. An electrical cylinder driven by a second servo drive presses the cap against the chair roller. A compression force sensor detects the surge in force when they engage. Together with the absolute position sensor system on the servo motor, it detects whether the pressing process was successful. The third servo drive controls the horizontal movement while the finished parts are set down on the chute, where the wheels, which are now appropriately protected, are transported to a lattice box and can be transported for further assembly.
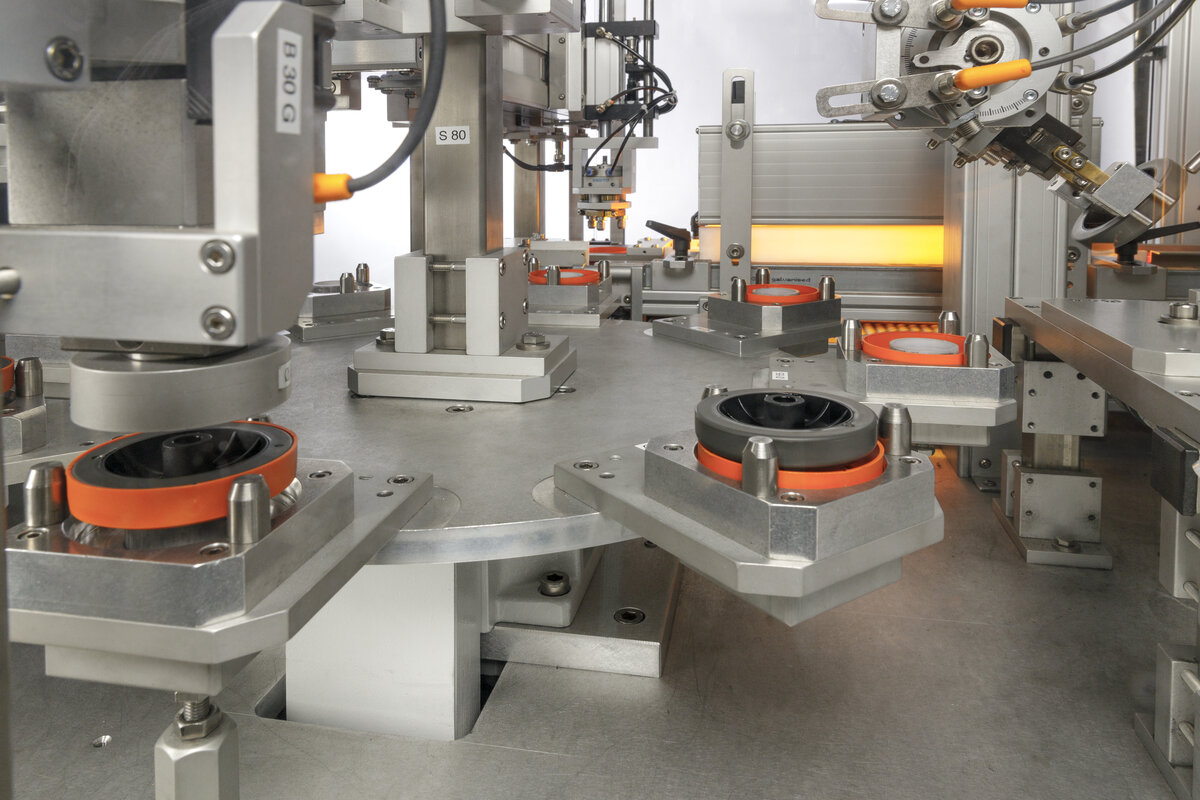
Drives, controller and software from a single source
The machine controller communicates with the servo axes via Profinet. This SLIO-series controller, which is also supplied by Yaskawa, can be programmed conveniently in Siemens Step7 and can be effectively adapted to the application thanks to its modular design. It was easy to add and interlink the additional I/O modules required; in principle, subsequent expansions are also possible. Additional speed benefits are provided by the backplane bus of the I/O system, which operates at 48 Mbit/s and enables field-bus independent switching with a timing accuracy of +/-1 μs. Short cycle times during program processing ensure rapid sequences. Integration into the application also facilitates the extensive system library of the controllers, with a large number of stored functions that can be enabled as required. This is particularly helpful when revising original designs, especially if you want to continue using an existing fieldbus. Profibus is a typical example of such a scenario.
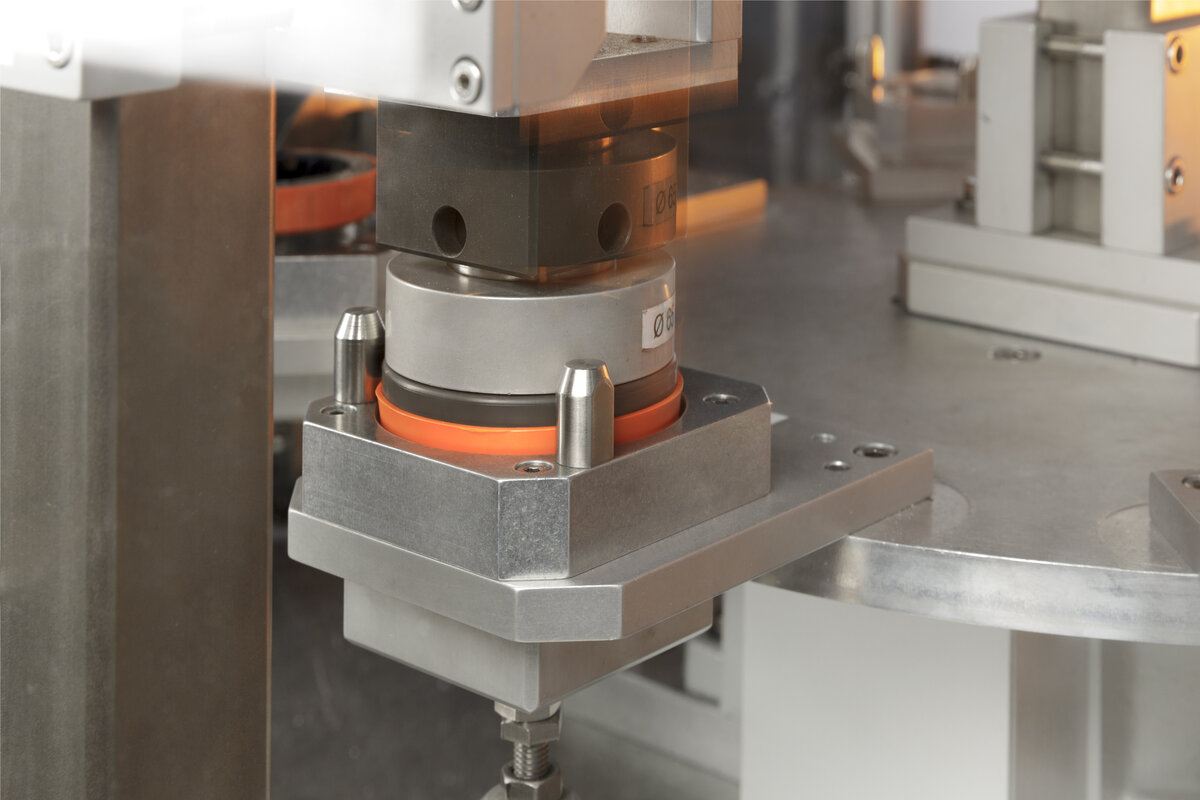
Yaskawa’s automation specialists were also a real help to the machine builder and its electrical design partners when it came to software adaptation. For instance, they assisted in integrating pneumatics, visualization and communication with the image processing system that Gross+Froelich uses for quality assurance. This “single source” principle meant commissioning was quick and straightforward. The hardware and software are perfectly adapted to each other and the machine builder had just one contact person. No one had to worry about interface issues and the bureaucracy or lost time they involve. The modernized machine and the components installed within it have proven themselves in practical application in the meantime, ensuring that countless chair castors are being provided with protective caps. The highly dynamic servo axes and powerful compact controller are making their own daily contribution to doing so.