Coffee to go with highly dynamic AC drives
Can you think of any other day-to-day product for which the demands for practicality are as great as the paper cup? With a paper cup machine from the BMP 100 series that produces up to 180 cups per minute, Michael Hörauf Maschinenfabrik provides a quality guarantee. A powerful inverter drive from Yaskawa ensures a particularly high level of control despite heavy electrical and mechanical loads.
- Industrije
- Živilska industrija
- Stranka
- Michael Hörauf Maschinenfabrik GmbH and Co. KG
- Izdelki
- GA70C - GA700 Series
Highly dynamic inverter drive ensures the highest control quality
The coffee “to go” tastes of freshly ground beans. The hot drink warms your stomach without burning your fingers, and can be enjoyed without spilling a single drop. Even though we don’t often pay a great deal of attention to paper cups, they must fulfill high quality standards day after day. At the same time, billions of identical products have to be produced in a cost-efficient manner.
The machines that make it possible to meet these demands are provided by Michael Hörauf Maschinenfabrik GmbH and Co. KG, a traditional company based in the Swabian town of Donzdorf. In addition to high-end machines for the efficient production of paper cups, the company’s portfolio also includes individual solutions for branded companies for in-house production of laminated paper packaging.
The BMP 100 Compact from the BMP 100 machine series is designed to economically produce cups for hot and cold beverages (e.g. coffee). In contrast, the BMP 100 Super is designed to produce large-volume packaging cups (e.g. for snacks, popcorn, noodles). Both machines can work both on the blank (paper segment) and on the roll. Depending on the size, cycle rates of up to 180 cups per minute can be achieved. The company’s expertise is based on many years of experience and a broad knowledge in the field of reshaping and joining paper or paper composite.
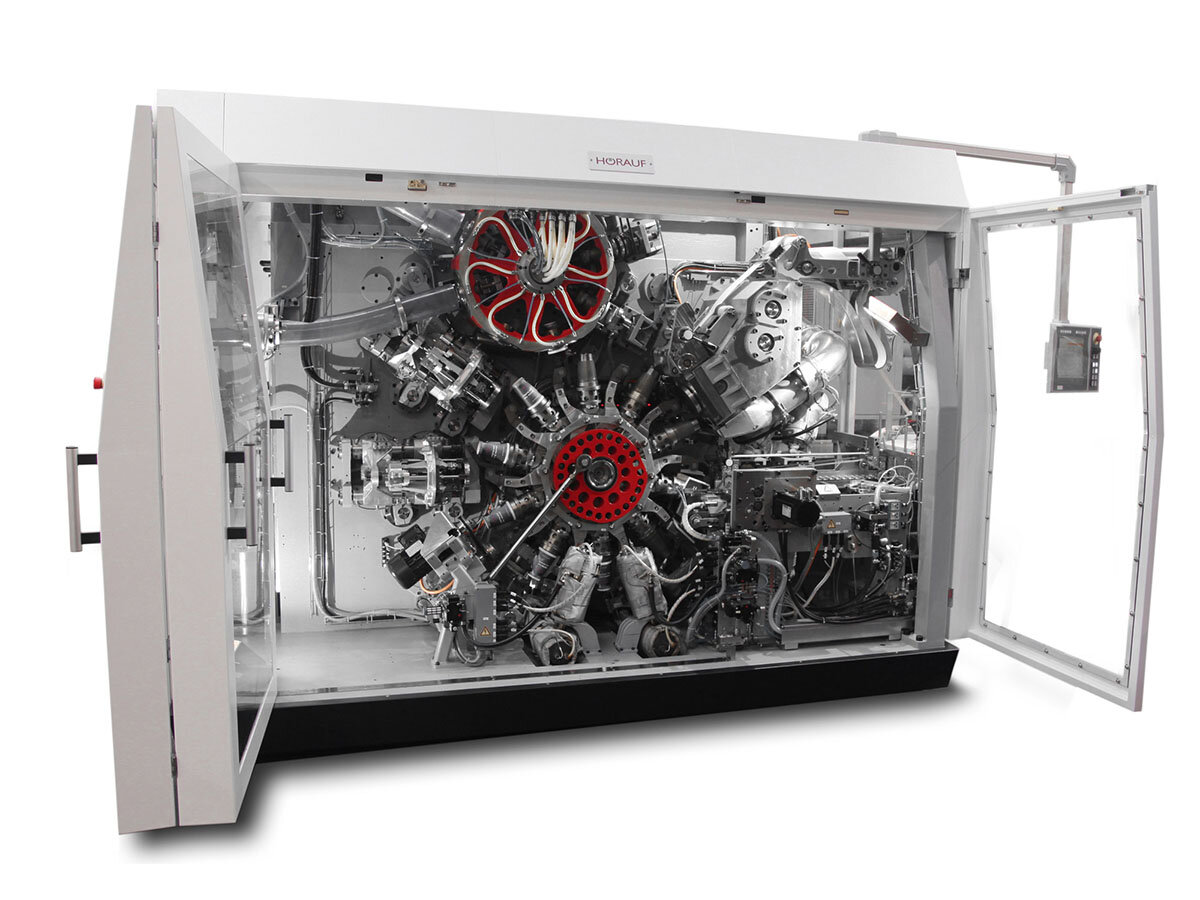
Drive engineering challenges
The centerpiece of the machine is the cup-shaped unit or “star.” This unit has a diameter of approximately 1 m and is equipped with core spikes. The unit must be accelerated and decelerated during each of the 180 cycles per minute. This mechanically demanding drive task is handled by an induction motor.
There were two issues that frequently occurred as a result of the regenerative operating states during the braking processes: Firstly, voltage surges put a heavy strain on the drives and thus led to failures. Secondly, the regenerative energy was converted into heat during braking, as a result of which the braking resistor temperatures rose to 80°C. Due to the use of highly flammable paper, it was not possible to install the braking resistors outside the control cabinets. The excess heat therefore had to be discharged from the control cabinets at a significant cost.
In light of this situation, Hörauf designers set out to find a suitable drive solution that would satisfy the high mechanical requirements without generating heat.
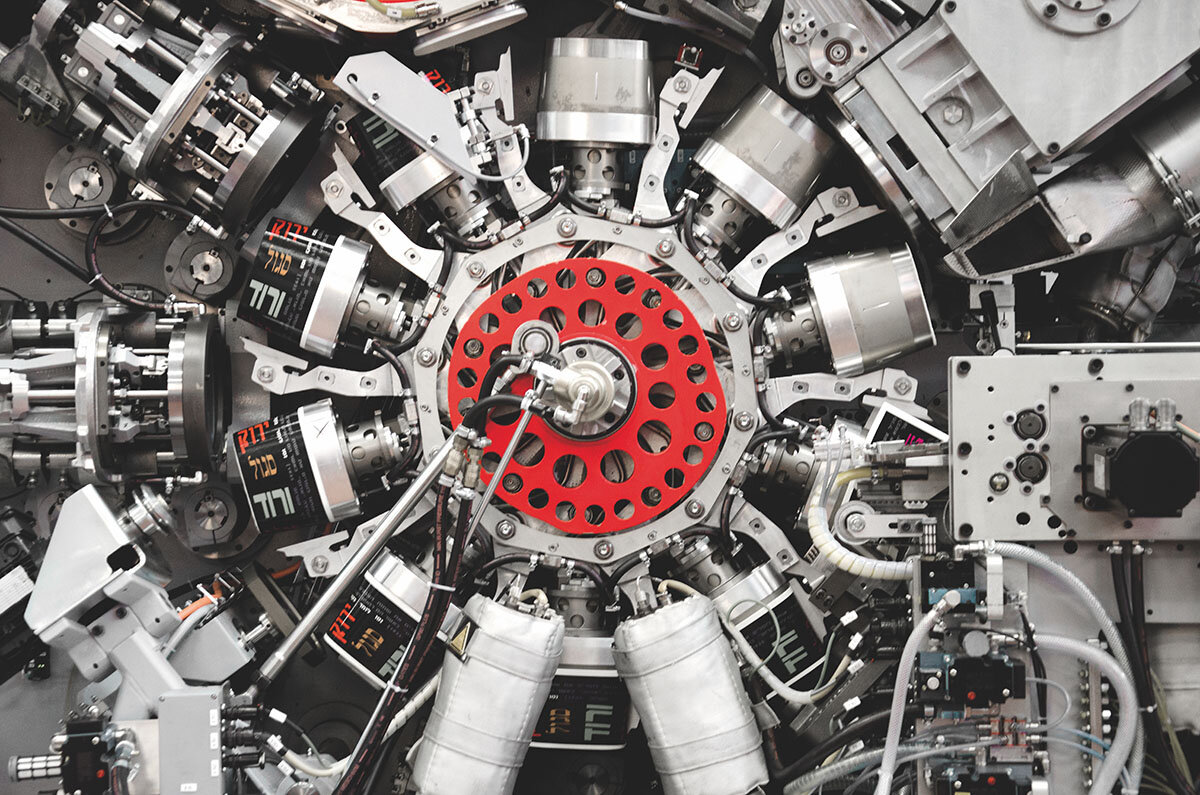
Solution: Inverter drive with open-loop vector control
The engineers at Yaskawa had just what they were looking for: The GA700 inverter drive, first introduced in 2015, offers the usual benefits of Yaskawa inverters as well as a number of other features: Load capacity, longevity and quality are ensured thanks to the design of the drives. The drives are designed to withstand ten years of continuous operation with a load weighing 80% of its maximum capacity. The drives operate at temperatures of up to 50°C without loss of performance. Users benefit from very low failure rates and minimal service effort.
In the above case, the use of a highly dynamic current vector control (open-loop vector control) also minimized the overshoot of the mechanics as well as the generative effects and voltage peaks. In concrete terms, the voltage peaks were able to be reduced by 30 percent, resulting in less regenerative energy. The temperature of the braking resistors now corresponds to the ambient temperature.
Induction motors and permanent magnet synchronous motors achieve full torque even at very low speeds without encoder feedback thanks to open-loop vector control. As the example of the BMP 100 Compact shows, the induction motor demonstrates a high control stiffness. The functionality of the GA700 combined with permanent magnet synchronous motors even mirrors that of servo drives.
GA 700 AC drive
In addition to the enhanced speed of the open-loop vector control, the GA700 inverter drive continuously optimizes its application parameters during operation. Thus, Yaskawa supports the engineers in planning, commissioning and operation through a variety of intelligent functions.
In terms of new features, the GA700 has an SD card slot, Bluetooth interface and real time clock. This allows accurate recording of load profiles or supports the service technician during troubleshooting, for example.
The GA700 can be quickly and easily started via the control panel, a PC or smartphone. The Yaskawa DriveWizard mobile app also makes it possible to save the parameters in the cloud or share them with other employees. This new concept means that the devices in the 700 series can be up and running in the minimum amount of time without the need for expert knowledge. They can also be operated very easily without considerable prior experience.
Thanks to integrated features such as the EMC filter, internal DC 24 V power supply with an additional 150 mA to power external sensors (e.g. temperature or pressure sensors) and functional safety in accordance with the STO SIL3 standard, the GA700 can also be used in higher risk applications without the need for external security measures.
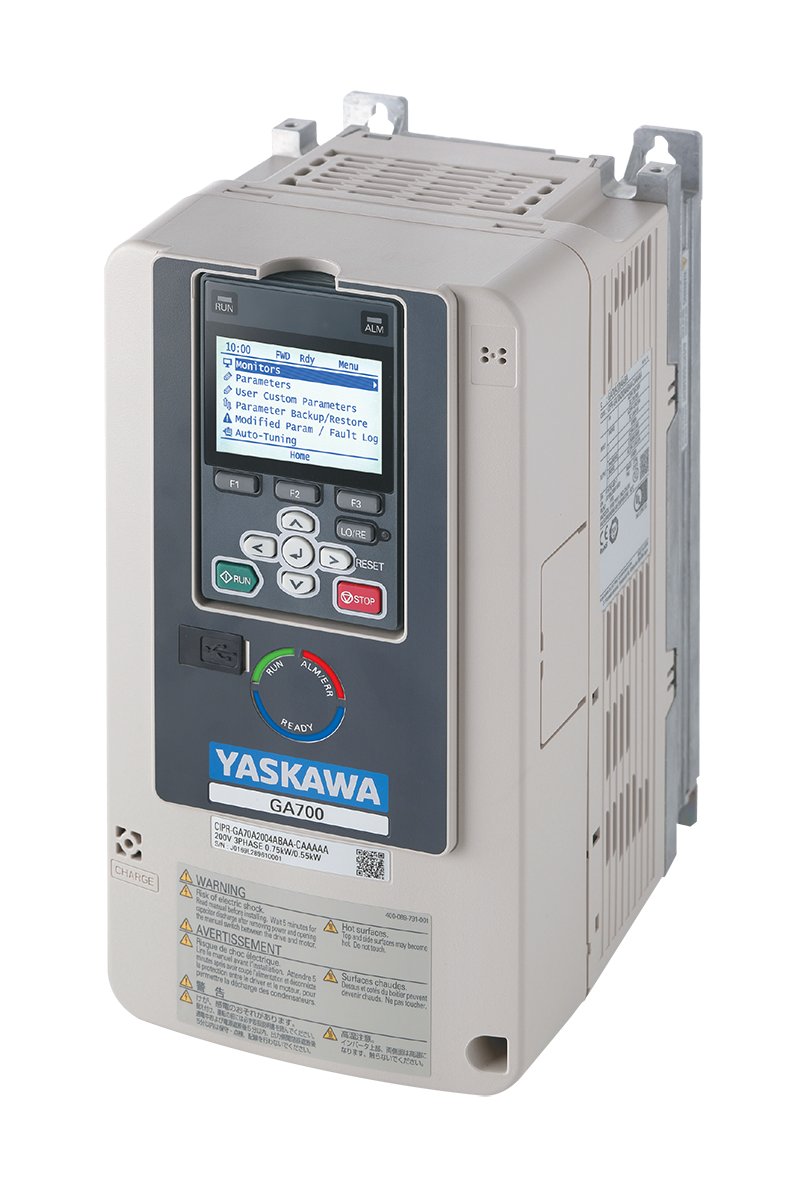
In conclusion
When a heavy cup-shaped unit with a diameter of 1 m is accelerated and braked 180 times per minute, the result is high mechanical loads and particularly high temperatures. By using the GA700 AC drive from Yaskawa, Michael Hörauf Maschinenfabrik was able to overcome this challenge. The use of these inverter drives resulted in a 30 percent reduction in cycle voltage spikes and a reduction in drive losses. In addition, the robust GA700 drive makes it possible to reduce the temperature of the braking resistors to ambient temperature, thus optimizing the cooling performance of the entire machine.